Sunlight Readability and Durability of Projected Capacitive Touch Displays for Outdoor Applications
November 2013
Sunlight Readability
Projected capacitive (PCAP) touch panels are rapidly replacing traditional mechanical methods of human-machine-interface in virtually every market, including outdoor applications. Touch panels are being designed into a variety of outdoor products, such as interactive kiosks, marine GPS systems and overall control systems for recreational watercraft and large ships. These rugged environments create unique challenges for designers of touch-enabled displays that need to perform consistently in these environments. In particular, the readability and durability of display systems that are exposed to direct sunlight for long periods must be addressed. Designing touch panels to work in rugged outdoor environments requires special considerations to overcome these challenges.
Although there are a number of display systems in the marketplace designed specifically for deployment in harsh outdoor environments, incorporating a PCAP touch panel creates a new set of design considerations, not only for the PCAP itself, but for the display system as a whole. Some of the features that are common to outdoor display systems include high brightness (> 800 nits), high contrast ratio and a wide viewing angle along with an extended temperature range. The brightness and contrast ratio help make the display more readable in outdoor conditions, and protective cover lenses with Anti-Glare (AG) or Anti-Reflective (AR) treatments are integrated with displays for enhanced durability and reduction of reflections. Adding a touch panel transfers the problem of reflection from the display to the PCAP cover lens, which is often part of the touch panel structure itself.
Surface Reflections and Air Gaps
When light strikes an interface between air and glass, or between air and an LCD display, roughly 4% of that light is reflected off the surface as a result of the difference in index of refraction between air and other materials. Such reflections will typically result in 10% to 15% total reflection for a touch panel bonded to a display with an air gap in between (Figure 1). The internal structure of the touch panel can also contribute significant additional reflections depending on its construction. To reduce the reflections that result from the air gap between the touch panel and display, a number of materials and methods are available for optical/direct bonding of the two. This type of bonding maintains a consistent index of refraction from the touch panel to the display and virtually eliminates all but the top surface reflections. Reducing these surface reflections on a touch panel adds an extra dimension of complexity. Designers must take into account the need for durability under hundreds of thousands, or even millions, of touches with the potential for abrasion from hard objects, such as jewelry, car keys, or any object someone might have in their hand while touching the panel. Over time, such abrasions can seriously degrade the optical quality of a cover lens, and even render it more susceptible to breakage.
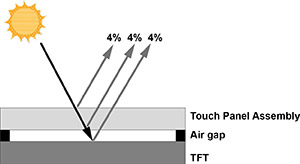
Figure 1: Reflections from a typical touch panel assembly with an air gap in between the touch panel and TFT.
Anti-Reflective (AR) coatings are a great way to reduce surface reflections on touch panel cover glass. Using the principle of destructive interference, vacuum deposited coatings with precise thicknesses and appropriately chosen indices of refraction can significantly reduce surface reflections down to 0.5% or better (Figure 2).
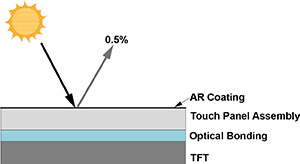
Figure 2: Reflectance is reduced to 0.5% when optical bonding is added to eliminate the air gap between a touch panel assembly and TFT and an AR coating is applied to the top surface
Lower cost coatings only have one layer that is designed for complete destructive interference of light with a particular wavelength, usually near the middle of the visible spectrum. While such coatings can significantly reduce surface reflections close to a specific wavelength, performance across the visible spectrum is poor and also results in a slight tint to the glass. Multi-layer coatings are more costly but dramatically reduce reflections from a variety of wavelengths (Figure 3).
For touch enabled displays with AR, it is essential to add an additional Anti-Smudge (AS)/anti-abrasion resistant coating to the surface because AR coatings have a tendency to attract fingerprints, are difficult to clean and have a lower surface hardness than glass. AS coatings are typically oleophobic and hydrophobic, meaning they resist the adhesion of oil and water, which makes fingerprints and contaminants less visible and much easier to clean without chemicals. These coatings offer enhanced surface hardness and low friction, which improves abrasion resistance when compared to AR coatings alone. Hydrophobic coatings are especially useful in marine applications since water will bead and run off the panel more easily [for systems not mounted horizontally], reducing the likelihood of large pools of water on the screen. Water pooling on the screen can cause performance issues for PCAP technology, especially if the water has a high salt content, such as seawater.
Another method for reducing the effects of reflections in outdoor displays is with Anti-Glare (AG) treatments. The term “anti-glare” is something of a misnomer, since glare technically refers to light incident directly upon the eye, such as direct sunlight, which reduces one’s ability to see an image or object. What AG treatments actually do is convert specular reflection to diffuse reflection (Figure 4).
The process for creating an AG surface typically involves etching the surface of the top glass layer. There are other techniques for producing an anti-glare surface, but acid-etching is the most common method for LCD and touch panel cover glass. Since AG treatments spread out reflections rather than eliminate them, they are quantified using Gloss Units (GU) instead of a reflection percentage. A glossmeter is used to measure the amount of light reflected at a specific angle (Figure 5), which is then compared to the amount of light reflected at the same angle from a standard surface of polished black glass with an index of refraction of 1.567, and this standard is assigned a gloss value of 100. Lower gloss levels indicate a more matte-like appearance. One of the disadvantages of AG is that as gloss decreases, haze also increases and image resolution is limited. The surface that diffuses reflections also diffuses the underlying image of the display. Another effect that is less quantifiable is sparkle, which is an appearance of varying brightness from one pixel to another. The amount of sparkle depends on distance, viewing angle and surface geometry. In selecting an AG treatment, it is necessary to compare samples from different vendors, as they can appear quite different while still yielding similar gloss measurements.
In addition to providing an anti-glare surface, the AG process also results in a surface that feels smoother when swiping or gesturing. Finger prints are less visible on an AG treated surface and they also wipe off more easily than on untreated glass.
Touch Panel Construction and Optical Properties
As mentioned above, the mechanical structure of a touch panel can have a significant impact on sunlight readability. There are a number of different projected capacitive touch panel structures in the marketplace, including all-glass (OGS, GG) and film based (GFF, G1F, etc.). The more material layers a sensor has, the more potential interfaces for reflections exist and care must be taken to minimize the difference in index of refraction from one layer to the next. Most PCAP sensor structures currently in production utilize either ITO on glass or ITO on film. Glass based sensor structures typically have the best optical properties, whereas film sensors must employ special index matching and anti-reflection layers within the layer structure to minimize internal reflections. However, some of the ITO replacements that are in development tout much better optical clarity than ITO on film, thereby eliminating the need for these extra layers, and providing optical performance on par with glass sensors.
Regardless of the conductive material, the majority of film based sensors are made with PET film, which introduces additional complications for outdoor applications. Many transparent materials, including glass, are optically isotropic, i.e. the index of refraction is not dependent on the angle of incident light relative to the material. PET film, however, exhibits birefringence, meaning that the molecular structure has an optical axis and light rays not aligned with the optical axis will be double refracted into two orthogonal light rays, each experiencing a different index of refraction, and therefore a different velocity. When a birefringent material is placed between two crossed polarizers, the difference in velocity of the refracted light rays can cause destructive interference and produce a rainbow effect (Figure 6). This presents a problem for outdoor displays with a touch panel situated between the front polarizer of an LCD display and a user wearing polarized sunglasses. Not only do ITO films often have this problem, but even glass-glass sensors will exhibit this phenomenon if birefringent laminates are used. Manufacturers are working on, and some currently offer, optically isotropic films for sensor structures to mitigate this problem.
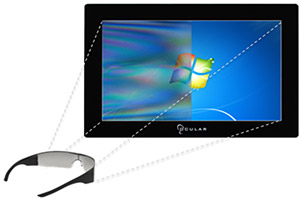
Figure 6: Comparison of different touch panel constructions using birefringent materials (left side of panel) vs. non-birefringent materials (right side of panel) when viewed with polarized sunglasses.
Durability
There are several challenges to overcome when designing a touch panel to survive in an outdoor environment. There are tradeoffs between the method used to reduce reflections and surface durability as well as between the sensor construction and resistance to solar radiation. As stated earlier, Anti-Reflective treatments need to be coupled with Anti-Smudge and anti-abrasion coatings. However, while these coatings reduce surface friction, which can help resist scratching, they range in hardness usually from 5H – 8H pencil hardness, which still isn’t as hard as glass. While there are MIL specs for coating durability, they aren’t for coatings that are intended to be touched aside from cleaning and environmental exposure. It is not uncommon for touch panels to have specifications requiring millions of touches and there isn’t much data about the durability of AR/AS coatings under these conditions. Additionally, outdoor applications that are in a marine environment (ex. Kiosk near a coast, boat GPS, etc.) require the ability to withstand salt mist exposure without hazing over, and again, many AR coatings aren’t sufficient, or haven’t been tested, to survive in such an environment.
Since AG glass is still just glass (i.e. no coating), the durability and surface hardness of glass is retained, but AG treatments aren’t as effective at reducing reflection as AR and have clarity/resolution issues as gloss level decreases. The AG process is also easier to incorporate with chemical strengthening of glass. For low to medium volume applications, it can be difficult to find vendors that provide chemically strengthened glass with an AR coating, depending on their processes. This is an issue because outdoor applications usually require a chemically strengthened top glass layer, either soda-lime or high-ion-exchange, for durability.
When extreme ruggedness or vandal proofing are required, the sensor structure must be taken into account as well. Touch panels with a dedicated cover glass offer the most options for cover glass type and surface treatments. One-Glass-Solution (OGS) or touch-on-lens type touch panels cannot be made from the strongest of the high-ion-exchange glasses because of the need for cutting and machining the sensor glass post-strengthening.
The types of laminates, ITO films, and optical bonding material must also be given careful consideration as some common materials may yellow after prolonged exposure to sunlight. Since sunlight exposure can also damage LCDs via UV exposure and IR heating, touch panels can be built with additional layers that reflect IR or UV light, which may eliminate the need for costly and bulky active cooling solutions in outdoor touch enabled displays.
Summary
As projected capacitive touch panels become the interface of choice in products that must survive long-term usage in outdoor environments, care must be taken when designing and/or selecting the appropriate PCAP. There are several interrelated design elements and tradeoffs that must be balanced. Optical bonding of the chosen PCAP to the display can greatly improve sunlight readability. Some bonding materials provide a gel-like bond that also improves impact resistance; however, this method of bonding can also add substantial cost, especially for large displays. Anti-reflective coatings on cover glass also greatly improve sunlight readability, but long-term durability in touch applications can be an issue and more industry testing needs to be done. Anti-Glare treatments also reduce the effects of reflections in bright sunlight and retain the durability of the glass surface, but can have a negative impact on the display image. The physical construction of the PCAP is important as well. If the end product will often be used in bright sunlight, the system must withstand many hours of solar radiation without yellowing and users wearing polarized sunglasses need to be able to read the display clearly. In marine applications, resistance to salt mist is also important and can impact which surface treatments are chosen to reduce reflections. It is imperative to discuss the environment in which the touch-driven device will be deployed during the initial design phase. Touch panel designers can recommend the appropriate coatings and stack-up required to enhance performance and overcome any external challenges caused by the environment.
Contact Us for more information.